Lighting Design & Installation .
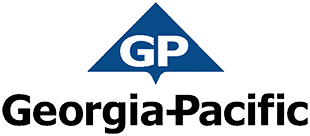
The Problem.
In 2019, Georgia Pacific’s Green Bay, WI, facility underwent a plant-wide initiative to save energy while delivering more candlepower to the plant floor. That meant converting from traditional lighting to high-efficiency LEDs. As the manufacturing engineer responsible for the buildings that house Paper Machines 7 & 8, the initiative posed several significant challenges for me and my team.
> Old lights were located directly over the paper machines
From a safety standpoint, we couldn’t have people in lifts up there while the machines were operating.
> Didn’t want to incur any extra downtime to get the job done
Our planned outages occur every 9 weeks. And the schedules for the two machines are staggered. Since the cranes for Paper Machines 7 & 8 overlap above Machine 8, that added to the logistical headaches.
> Needed a safe, practical solution for both installation and long-term plant maintenance
The buildings for Paper Machines 7 & 8 are high-temperature, high-humidity environments. Things that are overhead, like exhaust fans, sprinklers and lighting always seem to rust out and eventually fail. So, I didn’t want the lighting directly over the paper machines. I also wanted to avoid the time, expense and risk of using overhead lifts to do any maintenance of the lights down the road.
On top of that, I didn’t want to have to resort to performing lighting maintenance during our planned shutdowns. There are always so many people moving around the paper machine and building during the outages. I didn’t need big lifts getting in everyone’s way or posing any additional potential hazards.
The Solution.
We threw some big challenges Wasmer Company’s way, but their entire team really made the effort to work with us. The results were worth it.
> Collaborative design met our objectives
To get the job done, the way we wanted it and needed it to be done, Wasmer made use of the overhead catwalks that ran throughout both buildings. By mounting the new light fixtures within reach of the catwalks, we gained the convenient access we wanted but never had before. As a result, we could handle maintenance on our terms and on an as-needed basis. Wasmer helped us eliminate the need for lifts and the need to perform maintenance during our planned outages. It’s a lot safer and more convenient for our maintenance staff.
> Implementation flexibility involved strategically coordinated scheduling
During the planning phase, Wasmer told us how much time would be needed to perform the changeover. I pointed out that committing that much time all at once would be problematic to our production schedules. So once again, they worked with us to find a viable solution. Wasmer coordinated their work schedules around our scheduled production runs. During our changeovers between runs, the overhead cranes were locked down and Wasmer went to work. This close coordination meant the job got done efficiently and as planned – without creating any additional downtime.
> Custom configuration involved
In order to make the LED light fixtures accessible via the catwalks, Wasmer Company had to engineer and fabricate custom brackets. They also used stainless steel for the brackets to help prevent corrosion.
> Innovative, Military-Grade LED Lighting incorporated
Wasmer Company understood that our high-temperature, high-humidity environments could quickly compromise the performance and life expectancy of typical LED lighting solutions. So, they went with light fixtures that are documented to stand up to demanding environmental conditions. We’re definitely looking forward to the projected longevity compared to what we had in place.
The Results.
maintenance time
production line downtime
productivity + throughput
What We Do.
Sustainability.
Our Clients
Building Partnerships.
When you entrust us with a key to your plant, we don’t take it lightly. Every step forward is taken with care, diligence, and a sharp mind. Thank you for the opportunity to build solutions, business, and friendships.